Yapı malzemesi olarak kerpicin alçı ile stabilizasyonu TUBİTAK MAG-505 araştırma projesi kesin raporu,
Dr. Bilge IŞIK Istanbul Technical University, Architectural Faculty, Türkiye
1. INTRODUCTION
Since the industrial growth, the buildings have been constructed with the industrialized materials. The industrialized construction materials such as cement, steel etc. embodies energy and are polluting the environment. It is considered that living in buildings, constructed by industrialized material is comfortable and part of the growth. But without the heat insulation and vapor barrier layers that are to be placed carefully, human cannot survive in the reinforced concrete, metal or brick walled indoors. The layers of heat insulation and vapor barrier are energy consuming as well, expensive and labor intensive. The industrialized construction material has remarkable function on the increased environmental impact.
The World Commission on the Environment and Development suggested the definition 1987,
Sustainable development is the development that meets the needs of the present
without compromising the ability of future generations to meet their own needs.
Sustainability requires resources to be conserved, the environment to be protected and healthy environment to be maintained (Kibert Ch. J., 1994): The main resources to be conserved are the life, land and raw materials, including energy, water and air (G. Sebestyen, 1998)
The production of earthen construction material needs low-energy and the indoor environment created by that material is healthy. Earthen wall provides the house and living environment with load bearing capacity as well heat insulation, heat conservation and vapor diffusion values. Earth is most used construction material. 1/3rd of the world’s population and 28% of the rural people in Turkey are living in earthen architecture
In order to achieve sustainability, without sacrificing the comfort and growth, earthen construction technology has to be made applicable for the housing sector. To improve the properties of the earthen wall material, researches have been carried out at Istanbul Technical University since 1978. The new mixture was called ALKER, the short name of gypsum (alçı) and adobe (kerpiç) in Turkish respectively. The properties of alker are the indicator of the sustainable habitat by conserving the resources, protecting and maintaining the environment. Based on findings of the ongoing studies at Istanbul Technical University this paper provides a survey of the laboratory studies, informs about the findings of the pilot buildings and provides suggestion on a future strategy for a sustainable habitat.
2. LABORATORY STUDIES
The first researches started by improving the properties of the earthen wall material. Studies of the written documents enlightened, some admixture like cement, asphalt or organic materials can be put into the earth to improve the durability of traditional adobe. There was no sufficient document on gypsum stabilising. Gypsum and lime mixture on the historical building in eastern Anatolia has shown a significant durability. The research at Istanbul Technical University focused on gypsum stabilization since 1978.
Table 1. Advantages of the alker
The water sealing property improves
Mechanical properties improves
Low shrinkage
Clean surface
Short hardening (hydratation) time
2.1. Proportioning the alker mixture
The elements of the mixture are soil, gypsum, lime and water. Soil for alker is different than the traditional clayey adobe soil. Clay content is small, so that kind of soil can be found easily.
Table 2. Proportions of the mixed components (%)
Soil 100
Gypsum 10
Lime 2
Water 20*
(* According to the dryness of the soil)
Lime in the mixture enables the workability. If the content of lime increases the compressive strength decreases in the early ages dramatically; if the content of gypsum increases the compressive strength rises slowly. 10% of gypsum is the optimum amount considering the cost/benefit ratio.
Touching the water, gypsum strips in a short time. The stripping time of 3-8 min is not enough for working with the material. Lime is easily available material for retarding the process to 20min.
The production of alker starts by mixing lime in to the water firstly and gypsum secondly. This heavy water has to be poured onto soil and mixed mechanically about 3 min (by hand a little longer). It is not sufficient having the dry mixture before and pouring the water later. Water can cause rapid and inhomogeneous binding in the dry soil. Percentage of the admixture is to be seen in the Table 1.
Soil
For the use of traditional adobe soil must contain 24-30% clay. Max grin size has to be 20mm. Soil for alker contains about 8-10% clay, can be rich of silt and the diameter of gravel can rise up to 5-7cm. Topsoil with the rest of the plants should be removed and saved for the garden uses. If the foundation soil of the building is not enough for the building, excavation soil from foundations of the other constructions can be used for the alker walls. Most of the time there is no need for preparation of the soil, like sieving, grinding and leaving to rest (laying aside) after wetting
Obviously soil is not homogeny, so the properties change a lot. Table 4 gives an approach to the properties of the alker soil. Best selection is to look for a stable soil. Local tests with small amount of sample can show whether the soil is stable or not. Testing methods are universal, can be found in every technical book. .
Table 3. Behavior of the Minerals in the Clay
Kaolinite at the edge negatively charged stable in contact with water
Fixing capacity is low
Illite negatively charged not particularly stable in contact
Bond the sheets with water
Montmorillonite not electrically neutral suffers from swell
Sheets are weakly connected in contact with water
Table 4. Properties of earth sample adequate for alker
Kafescioglu and others, 1980
Liquid limit % 35.50
Plastic limit % 27.50
Plasticity % 8.00
Shrinkage% 15.00
pH 5.90
Unit volume weight gr/cm2 2.75
Color khaki
Element %
Gravel -----
Sand 45
Silt 27
Clay 3
Basic clay mineral Kaoilnite
2.2. Mechanical Properties
Table 5. Mechanical Properties of Alker
Compressive strength 2.0-4.0 N/mm2
Shear strength 0.9-1.3 N/mm2
Compressive strength min 2.0 N/mm2
Of SIA, (Schweizerischer Ingenieur-und
Architekten Verein) standards
Table 6. Earthen Wall Material Curing Comparison
To obtain the Required Strength
Without stabilizer gypsum/lime
Stabilizer
Strangening in strangening in
15-20 days 20 min
Curing area not necessary
Water sprinkling not necessary
Rain protection not necessary
2.3. Physical properties
Table 7. Physical Properties of Alker
Unit weight 1.6-1.7 kg/lt
Shrinkage 1-1.5 %
Water absorption Very low
Long term water exposure No erosion
Heat transfer value l 0.4-0.5
Specific calorific c 1.0 kJ/kgK
2.4. Environmental Properties
The lifecycle of alker construction has a low impact on environment. Raw material supply consists of excavation and transportation of the proper soil to the site. Energy consumption of the procurement is low. Kiln energy of the gypsum and lime is lower compared with cement, resulting less Material production energy. At the material production level, to meet such a comfort created by alker wall, several layers are required, which are resource consuming and labor intensive. Alker construction process is furnished with equipment such as mixer and compactor. Energy consumption is low due to shortened process time, enabled by gypsum stabilization. . Maintenance can be avoided by reasonable design of the construction. After demolishing the alker house the wall material is biologically safe and degradable.
In the housing sector most of the energy is used for heating. During the service life of an alker house, the heating energy is low, thanks to its low heat transfer value l=0.4 kcal/mK, resulting from the research on the first pilot building. The 18-month lasting measurements summarized in the report Kafescioglu 1987.
The climate of the area where the fourth pilot building was built is hot in the summer and could in the winter. Investigations carried out, to compare the self-help-housing material, which are hole brick and hole concrete block with the alker wall regarding the thermal properties and environmental impact. Figure 1.showes the daily temperature changes in the investigated area in winter and in summer.
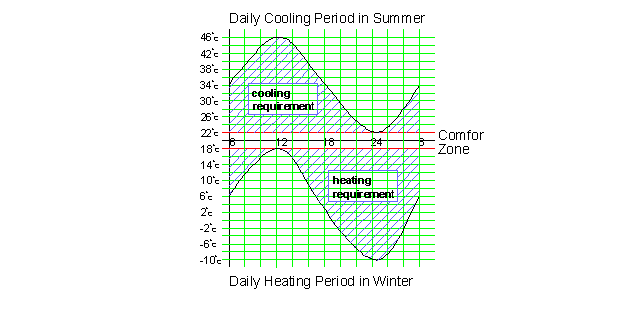
Figure 1.Daily heating and cooling period in the southeast Turkey
In the moderate climate like in Turkey the heating and cooling energy is about 75-82% of the energy consumption of a house (Table 8)). CO2, CH4, N2O and some particles are polluting the air more or less due consuming energy from the fossil resources like coal, oil or gas, during the life cycle of the building.
Table 8. Energy consumption of any given house in moderate climate
Heating 82%
Warm water 10%
Electric equipment 7%
Lighting 1%
Table 9. Heat loss proportions of brick building comparing with alker house parts
Window, door 37% 8.20%
Roof 15% 24.4%
Floor 13% 13.2%
Wall 35% 24.5%
Air circulation 10.8%
Energy and emission savings due changing wall material is remarkable. To illustrate the thermal response closely, and to compare the environmental impact of brick (19cm) and alker (45cm) wall in the climate area (Figure 1), calculations are carried on a local 100m 2 building. Depending the heat transfer value
Alker l=0.4 kcal/mK,
Hole load bearing brick (TSE 825) l=0.81-0.94 kcal/mK,
Savings of the emissions are (Işık 1998):
CO2 =98.1%, SO2 =56%, NOx=32%, CO=49%, CxHy =18%, Particle=39%
After the World Environment Conference Rio’92 and the others, the declarations pointed out, to decrease the CO2 emission to 50% until the year 2005, to slow down the global heating. Calculations regarding the thermal properties of alker showed that using alker contributes significantly.
3. FINDINGS OF THE PILOT BUILDING
3.1. Alker Pilot Building I., 1980
Figure 2. First alker building as kinder-garden of the University
First Alker building served as the kind-garden of the Technical University from 1983 to 1991. Hand made blocks are used for the masonry building. Ceiling is reinforced concrete. Outside walls are 45cm and inside walls are 30 cm thick, both load bearing. Kitchen and bathroom walls are covered with tiles, using cement mortar. Vapor diffusion is significant for the durability of the plaster. Walls from inside are covered with gypsum plaster and from outside earth-lime-sand mixture. Floor heating is installed under the floor tiles. Findings are as:
Alker building is suitable for any utility services.
SUMMARIZING
Based on findings of the ongoing laboratory studies on gypsum and lime stabilized earth at Istanbul Technical University, the compressive strength raises to 2-4 N/mm2 and shrinkage goes down from about 5% to 1%. The heat loss value is l=0.4 kcal/mK, which provides energy savings and healthy indoor environment.
The findings of the four pilot buildings inform that Alker material can be constructed individually or collectively and provides the housing demand. In other words it can be constructed labor intensive or with mechanical equipment.
Alker building is suitable for ultimate housing needs and for any utility services.
The need is the legislative and administrative support of the efforts and strengthening of the existing financial mechanism. Affords of Istanbul Technical University are to foster the certainty to the new material alker, with ongoing researches, to maintain the future strategy for a sustainable habitat.
REFERENCES
Işık B., Akın A., and others., 1995: “Mechanization of the Gypsum Stabilized Technology” TÜBITAK INTAG TOKI (Turkish Scientific and Technical Research Institute) Research project 622,
Işık B., 1998 “Earth as a Wall Material and its Impact on Pollution” CIB World Building Congress’98, Gaevle,
Kafescioglu R., 1984: “Gypsum Added Stabilized Adobe (ALKER) for Rural Housing. International Colloquium on Earth Construction Technologies, Appropriate to Developing Countries. Brussels, Belgium, December 10-19, 1984
Kafescioglu R., 1987: “Thermal Properties of Mud bricks” Amman Expert Group Meeting on Energy-Efficient Building Materials for Low-Cost Housing.
Kibert Ch. J., 1994: “Sustainable Construction” Proceedings of CIB TG 16 Conference, Tampa, Florida, USA, 6-9 November 1994
Sebestyen G., 1998: “Construction Craft to Industry” E&FN Spon SIA D0111.,1994, “Regeln zum Bauen mit Lehm ” Standards from (Schweizerischer Ingenieur-und Architekten Verein)
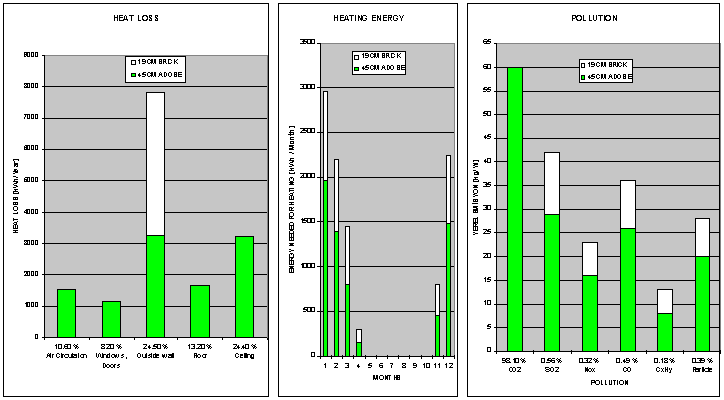